Unlocking the Power of Metal Stamping: Strategies for Enhanced Product Advancement
In the realm of production, the utilization of metal stamping holds a significant area due to its convenience and performance in generating detailed components and components. Nevertheless, the real possibility of metal stamping stays untapped by many business looking for to boost their product advancement processes. By discovering sophisticated approaches and methods tailored to enhance layout, product choice, production efficiency, and quality assurance, companies can open a wealth of possibilities to raise their products to new elevations of innovation and efficiency.
Advantages of Metal Stamping
Steel marking offers a reliable and cost-effective approach for producing top notch metal parts. This manufacturing procedure includes shaping, cutting, or forming steel sheets utilizing a marking press (Metal Stamping). One of the key advantages of metal stamping is its capacity to produce complicated geometries with high accuracy and uniformity. This is specifically helpful for industries such as auto, aerospace, and electronic devices, where intricate metal components are often needed.
Moreover, steel marking enables high-volume manufacturing, making it suitable for projects that require big quantities of steel parts. The speed and repeatability of the marking process not only make certain price financial savings yet additionally contribute to faster turn-around times for production orders. Additionally, using automatic tools in metal stamping aids reduce the danger of human mistake, causing enhanced total item top quality.
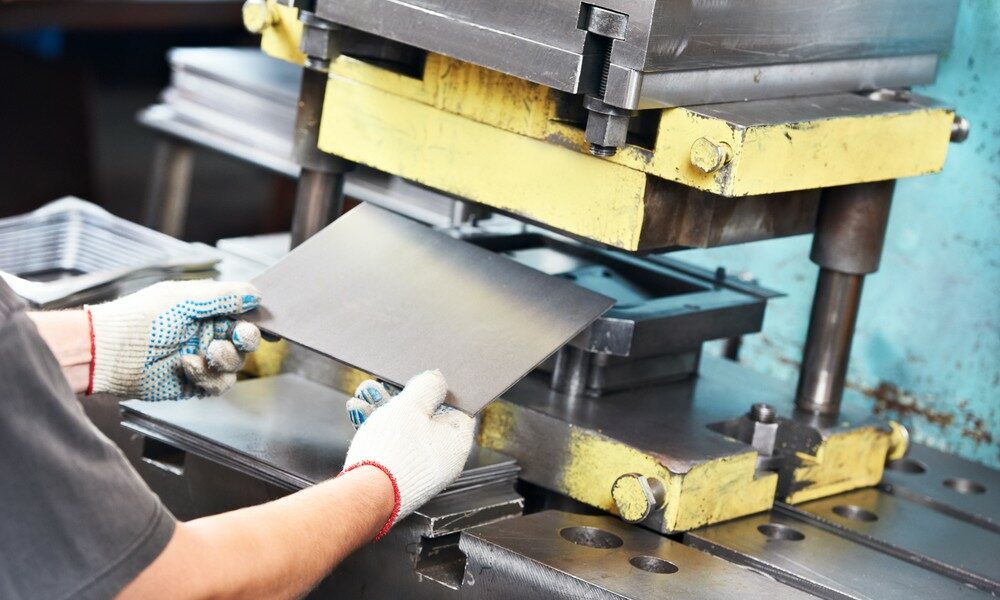
Design Optimization Methods
Via cautious factor to consider of product residential or commercial properties and geometric setups, layout optimization techniques play a crucial role in boosting the performance and functionality of steel marking procedures. By purposefully analyzing factors such as product density, stamina, and kind, producers can customize the layout to take full advantage of the performance of the marking operation. Using simulation software program, designers can predict just how different style variations will certainly act under different stamping problems, enabling for the identification of potential concerns prior to manufacturing starts.
Furthermore, incorporating features like fillets, chamfers, and embosses right into the layout can enhance the general quality of the stamped component while reducing the danger of issues such as cracking or warping. In addition, maximizing the design of features on the component can improve the product circulation throughout marking, leading to even more exact and constant results.
Fundamentally, layout optimization methods allow producers to tweak their steel stamping procedures, leading to improved item top quality, raised manufacturing efficiency, and inevitably, an extra affordable position in the marketplace.
Product Option Methods
Design optimization techniques in metal marking procedures greatly depend on strategic material selection strategies to make certain the wanted efficiency and performance of the produced parts. The choice of product in metal marking is critical as it straight affects the high quality, toughness, and overall performance of the final product. When selecting the ideal material for a specific project, factors such as mechanical residential properties, formability, corrosion, and cost-effectiveness resistance have to be taken right into consideration.

Furthermore, cost-effectiveness plays a significant role in material choice strategies. Balancing the performance requirements with the total price of materials is vital to make sure the economic viability of the manufacturing process. Furthermore, considering elements like recyclability and environmental influence can even more boost the sustainability of the chosen material. By very carefully reviewing these aspects, suppliers can optimize their material choice strategies to accomplish see this remarkable product high quality and operational effectiveness.
Enhancing Manufacturing Performance
Performance in manufacturing procedures is an important factor for ensuring cost-effectiveness and timely delivery of top notch metal marked components. To enhance manufacturing efficiency in metal marking, several approaches can be implemented.
Furthermore, applying automation and robotics in steel stamping procedures can dramatically enhance productivity and consistency while reducing labor prices. Automated systems can carry out repeated jobs with high accuracy and rate, resulting in improved production effectiveness and greater output prices. Spending in contemporary marking tools with innovative attributes, such as servo-driven presses and quick die modification systems, can even more optimize production procedures and decrease downtime.
Furthermore, developing clear interaction channels and promoting cooperation between engineering, manufacturing, and style groups is important for identifying potential traffic jams and carrying out constant improvements in the manufacturing workflow - Metal Stamping. By welcoming lean production principles and leveraging modern technology developments, suppliers can unlock the complete possibility of metal marking processes and achieve greater manufacturing efficiency
Quality Assurance and Evaluation Approaches
To ensure the regular production of top notch metal stamped parts, extensive quality assurance and examination approaches play a critical duty in validating the precision and stability of the manufacturing process. Quality control in metal marking involves a series of systematic checks and measures to ensure that each part satisfies the specified needs. Evaluation methods such as visual evaluation, dimensional analysis, and material screening are frequently used to analyze the top quality of stamped parts. Visual examinations make certain the surface finish and honesty of the parts, while dimensional analysis validates that the parts adapt the called for specifications. Product testing techniques like solidity testing and product make-up evaluation help validate the product residential or commercial properties and architectural honesty of the pop over to this web-site stamped parts. In addition, progressed technologies such as automated optical inspection systems and coordinate measuring equipments are progressively being made use of to enhance the precision and efficiency of quality assurance processes in metal marking. By executing durable quality assurance and assessment approaches, manufacturers can promote high standards of high quality and consistency in their metal stamped items.
Conclusion
In conclusion, steel marking deals many benefits such as cost-effectiveness, precision, and flexibility in product growth. Generally, unlocking the power of metal marking requires a critical strategy to boost item advancement processes.
Steel stamping offers a cost-efficient and efficient approach for producing top quality metal components.Additionally, steel marking permits for high-volume production, making it ideal for tasks that need huge quantities of steel elements.Via careful factor to consider of material residential or commercial properties and geometric setups, style optimization techniques play a vital role in boosting the effectiveness and performance of steel stamping procedures.Design optimization techniques in steel stamping additional hints processes greatly rely on calculated product choice methods to ensure the preferred performance and performance of the produced components. The selection of material in metal marking is essential as it directly impacts the top quality, resilience, and total performance of the final product.